Quality Management Tools: Essential Resources for Success
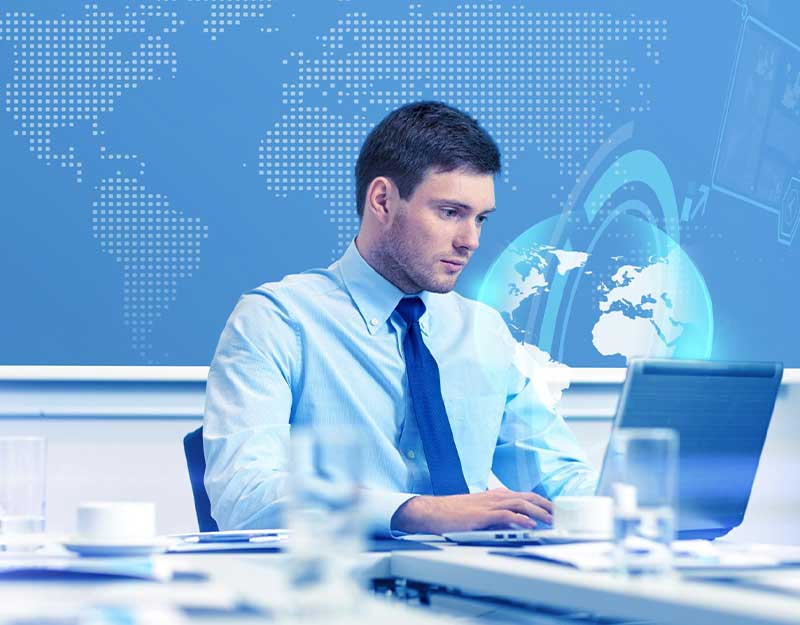
As the world becomes more competitive, delivering high-quality products and services has become a necessity. One of the biggest challenges for businesses today is consistently meeting customer expectations while maintaining operational efficiencies and reducing costs. Companies that prioritize quality can handle costly errors, dissatisfied customers, and a damaged reputation.
Here is where quality management tools and methodologies come into play. From Six Sigma’s data-driven approach to Lean’s focus on reducing waste and Total Quality Management’s (TQM) commitment to continuous improvement, these methodologies serve as essential guides for organizations aiming to excel. This blog will explore practical quality management tools that can help streamline processes, enhance product quality, and drive business success.
Six Sigma: Data-Driven Perfection
Six Sigma is a data-driven methodology that eliminates defects and improves process quality. It was developed to systematically reduce process variation and achieve improvements. The primary goal of Six Sigma is to achieve a defect rate of less than 3.4 defects per million opportunities, thus accomplishing near-perfect quality.
Six Sigma uses a step-by-step process called DMAIC, which stands for Define, Measure, Analyze, Improve, and Control. This approach believes that by following these five phases, any business can effectively solve even the most challenging problems.
Benefits of Six Sigma
Six Sigma offers a magnitude of benefits that can significantly enhance an organization’s performance:
- Reduced Process Variation: Six Sigma focuses on statistical analysis, which helps minimize variability and leads to more consistent outcomes.
- Enhanced Customer Satisfaction: Improved quality and reduced defects result in better products and services, increasing customer satisfaction.
- Cost Savings: Reducing defects and inefficiencies leads to substantial cost reductions and better outcomes.
- Data-Driven Decision Making: Six Sigma emphasizes the use of data, enabling businesses to make more informed decisions rather than relying on intuition.
Real-World Example of Six Sigma
Six Sigma is a powerful tool that helps improve efficiency and quality in any industry. Some of the Six Sigma project examples include:
-
Healthcare: Six Sigma can produce efficient medical records and improve patient satisfaction in the healthcare sector. It also helps minimize medication errors, improve patient safety, and reduce the length of stay in the hospital.
-
Manufacturing: Six Sigma's ultimate goal is to reduce variability and produce items without defects. It helps cut down lead times, enhance quality control processes, and lower scrap rates.
-
Finance: The finance sector can use Six Sigma for risk management, balance sheet management, and investment portfolio optimization. It can effectively reduce the time taken to process payments and lower the cost of credit card transactions.
-
IT/Technology: Six Sigma is frequently used by software developers looking to create high-quality, bug-free products. It can also be applied in project management to help reduce costs and enhance efficiency.
-
Automotive: Six Sigma was originally developed by Motorola to improve quality and reduce costs. General Electric later adopted it, setting it as a benchmark for quality improvement in the manufacturing sector.
Individuals seeking Six Sigma can click here and earn their certification in easy steps. These certifications from Knowlathon are awarded through a belt system, almost similar to karate training.
Lean: Eliminating Waste for Maximum Efficiency
Lean is a systematic approach that helps improve efficiency by eliminating process waste. Developed by the Toyota Production System, it emphasizes on continuous improvement while using fewer resources.
Lean methodology focuses on core principles such as Value Stream Mapping, which eliminates non-value-added steps in processes; Kaizen, the practice of continuous improvements and the 5S Framework (Sort, Set in Order, Shine, Standardize, Sustain), which aims to create an organized, efficient, and clean workplace. Together, these principles help reduce waste, streamline operations, and enhance productivity.
Benefits of Lean Methodology
Incorporating Lean can provide significant advantages to organization, including:
-
Reduced Waste: By identifying and eliminating non-value-added activities, Lean minimizes waste, leading to more efficient processes.
-
Faster Turnaround Times: Streamlined processes allow quicker completion of tasks while improving delivery times.
-
Cost Savings: Reducing waste and optimizing resource results in lower operational costs and increased profitability.
-
Improved Quality: Lean focuses on continuous improvement that helps enhance product and service quality by reducing defects and errors.
Real-World Examples of Lean
With implementation of Lean tools, businesses have achieved efficiency and production gains. Some of the real-life examples how Lean tools can improve operational performance include:
-
Automotive Parts Manufacturing: When an automotive company experienced losing production efficiency during shift changes, a lean consultant created a changeover that minimized downtime.
-
Cable Manufacturing: A cable manufacturing was able to reduce set-up times and shorten the lead time to market with an effective lean management approach.
-
Printing Industry: When a printing industry suffered with late orders and long lead times, a lean team was approached, which helped identify waste and maximize workflow.
-
Warehouse Management: A manufacturer found that their operational costs are high, including unloading, storing, and delivering materials. A lean team worked for them to design a point-of-use Kanban system to eliminate the large volumes of raw materials.
-
Customer Service: A manufacturer needed help keeping up with increasing demand. Management adopted lean techniques to eliminate waste and improve efficiency for on-time deliveries.
Get your Lean Six Sigma Green Belt Certification from Knowlathon by clicking here.
Total Quality Management (TQM): A Holistic Approach to Quality
Total Quality Management (TQM) is a collective approach to quality management that involves all employees in an organization. It emphasizes continuous improvement, customer satisfaction, and employee empowerment. TQM aims to build a culture of quality at every level of the business.
The key principles of TQM include customer focus, where every process aims to meet customer expectations; employee involvement, which encourages participation from all levels in quality improvement; and process optimization, which emphasizes continuously refining processes to reduce errors and enhance efficiency. TQM helps organizations build a quality culture by embedding these principles, fostering continuous improvement across all operations.
Benefits of TQM
Implementing TQM offers several advantages, including:
-
Culture of Quality: TQM creates an overall culture that prioritizes the quality of products and services, reducing defects and rework.
-
Increased Customer Satisfaction: By focusing on customer needs, TQM enhances customer satisfaction and quality.
-
Reduced Costs: TQM helps identify and eliminate waste, leading to cost savings.
-
Stronger Market Position: A reputation for quality make organizations competitive in the market.
Real-World Examples of TQM
Some of the most popular examples of TQM are:
- Healthcare Organization: TQM reduces costs, creates a higher level of efficiency and provides high-quality care to patients. Cost and good treatment are the keys to the hospital business. TQM takes care of appointment costs, medical treatment, and timely services, thus leveraging healthcare services.
- Multinational Companies: TQM can be an essential tool for MNCs. It helps monitor profit parameters. It ensures that the company monitors both employees and customers while dividing equal responsibilities among the team.
- TQM in Developing Economics: TQM is accepted globally and is implemented on a scale to help make more profits from various projects.
- Construction Industries: The construction process is expensive and requires a lot of effort. TQM helps reduce costs, boost productivity, and enhance overall performance by ensuring that every effort counts towards continuous improvement.
If you want to get TQM or other related certifications, contact Knowlathon.
Conclusion
This blog has explored three of the most essential quality management tools. Each approach offers unique strategies and helps enhance quality, reduce waste, and drive continuous improvement.
Those looking to implement these methodologies can seek professional training from Knowlathon to gain deeper insights and maximize the benefits of these powerful quality management tools.